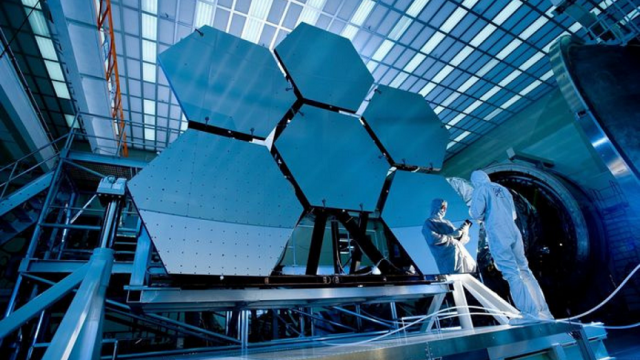
Elektronik für Positionssensoren
Lichteinfall präzise lenken
Spiegellenk- oder Spiegelablenksysteme sind in einer Vielzahl von Anwendungen vertreten, von der Luft- und Raumfahrt über Solarsysteme bis hin zur Halbleiterlithographie. Spiegel werden überall dort eingesetzt, wo Licht reflektiert und gelenkt wird, um auf einen bestimmten Punkt fokussiert oder gestreut zu werden. Dahinter steckt zunächst eine Mechanik, ein Motor, der ein oder mehrere Teile bewegt, die wiederum die Spiegel verstellen und auf das Licht passend ausrichten. So wird das Licht gebündelt und auf einen Punkt gebracht. Gesteuert wird diese Ausrichtung über eine Elektronik und bestimmte Positionssensoren, die möglichst präzise den Status der Spiegel an die Steuerung übermitteln müssen. Die auszurichtenden Elemente können dabei sehr unterschiedlich sein: z. B. riesige Photovoltaikelemente bei Solarkraftwerken, großformatige, aber auch sehr kleine Spiegel bei Weltraumteleskopen, bei denen die Auslenkung im Nanometerbereich vollzogen werden muss. Anhand der drei genannten Anwendungsbeispiele – Weltraumteleskop, Solarkraftwerk und Halbleiterlithographie – soll aufgezeigt werden, welche Anforderungen und Bedingungen es bei Spiegelablenksystemen zu erfüllen gilt.
Weltraumteleskop: kleine Ablenkung, große Wirkung
Angesichts der Entfernungen, die es bei der Nutzung eines Weltraumteleskops zu überbrücken gilt, könnte man meinen, dass es sich um große Spiegel und eine umfangreichere Verstellung dieser handelt. Tatsächlich geht es gerade in diesem Beispiel um eine nanometerkleine Ablenkung des auftreffenden Lichtstrahls. Zum einen gibt es Teleskope, die sich auf der Erde befinden und durch die ein winzig kleiner Punkt im Weltall beobachtet werden soll. Je größer hier die Spiegelausrichtung und -ablenkung ist, desto mehr entgleitet dieser winzige Punkt. Dahinter stecken einfache Winkelgesetze. Es handelt sich um mehrere Spiegel, die auf diesen Fixpunkt hin ausgerichtet und genau aufeinander abgestimmt werden müssen. Hinzu kommt der Atmosphäreneinfluss auf der Erde. Wenn zum Beispiel in der Atmosphäre Feuchte vorhanden ist, wirkt diese wie eine Linse und lenkt das Licht zusätzlich ab. Solche atmosphärischen Turbulenzen müssen über eine weitere minimale Auslenkung der Spiegel zusätzlich kompensiert werden. Aus diesem Grund befinden sich die meisten Spiegelteleskope in abgelegenen Regionen wie Wüsten und Erhebungen, um störende irdische Einflüsse bestmöglich zu vermeiden. Dennoch sind beispielsweise beim ELT (Extremely Large Telescope) in der chilenischen Atacamawüste 6.000 Aktuatoren zur Korrektur der atmosphärischen Turbulenzen im Einsatz, die ca. 1.000 Aktionen pro Sekunde ausführen.
Bei tatsächlichen Weltraumteleskopen wie dem James-Webb-Teleskop, die in einer Umlaufbahn der Erde ihre Dienste verrichten, sind die harschen Umgebungsbedingungen des Weltraums eine Herausforderung für Sensoren und elektronische Elemente: extreme Temperaturen, Vakuum und UV-Strahlung. Auch hier gilt: Wenige Nanometer Positionsveränderung sind entscheidend, um die verschiedenen Spiegel aufeinander abzustimmen. Die Ausrichtung kann hier sogar mehrere Tage oder Wochen in Anspruch nehmen. Zudem wird nicht nur sichtbares Licht gelenkt, sondern Wellenlängen bis in den mittleren Infrarotbereich, die ebenfalls präzise reflektiert werden müssen.
Solarwärmekraftwerke: Sonneneinstrahlung im besten Winkel nutzen
Bei Solarwärmekraftwerken kommt eine Vielzahl von Spiegeln zum Einsatz, um das Sonnenlicht zu reflektieren und in einem Punkt zu bündeln. Es handelt sich um riesige Anlagen in sonnenreichen Regionen, mit denen Strom erzeugt wird. Eine Variante der Anlagen sind Solarturmkraftwerke. Alle großformatigen Spiegel werden automatisiert der Sonne so nachgeführt, dass sie immer im bestmöglichen Winkel zur Sonneneinstrahlung ausgerichtet sind, um möglichst viel Sonnenlicht „einzufangen“ und auf den Turm oder Absorber in der Mitte des Kollektorfelds zu bündeln. Die Spitze des Turms erhitzt sich auf über 1.000 Grad Celsius und diese Wärme wird häufig zum Antrieb einer Dampfturbine genutzt, um so Strom zu erzeugen. Die Auslenkwinkel bei den Solarreflektoren sind deutlich größer als im Teleskopbeispiel. Möglich ist ein kombiniertes System aus einer Mechanik, die die Großauslenkung der Spiegel leistet, um die Sonnenbewegung zu kompensieren, während die punktuelle Fokussierung auf den Absorber zum Ausgleich von Windeinflüssen mit kleinen Ablenkungen der Spiegel über Positionssensoren gesteuert werden kann.
Herausfordernd für Positionssensoren und die enthaltene Elektronik sind die extremen Temperaturunterschiede, die in den sonnenreichen Gegenden, häufig Wüsten, auftreten: tagsüber sehr hohe Temperaturen (40 bis 50 Grad Celsius), nachts können die Temperaturen stark fallen (minus 10 Grad Celsius). Es muss gewährleistet sein, dass Sensoren bei einer solchen Temperaturspanne sicher und präzise funktionieren. Feuchte darf keinen Einfluss auf das Messergebnis haben, ebenso wie Verschmutzungen durch z. B. Staub. Je nach Anforderungen können für Abstandsmessungen der Spiegel kapazitive oder induktive Sensoren zum Einsatz kommen. Bei Feuchte und Verschmutzungen sind induktive Sensoren die bessere Wahl, da diese Bedingungen keinen Einfluss auf das Messergebnis haben.
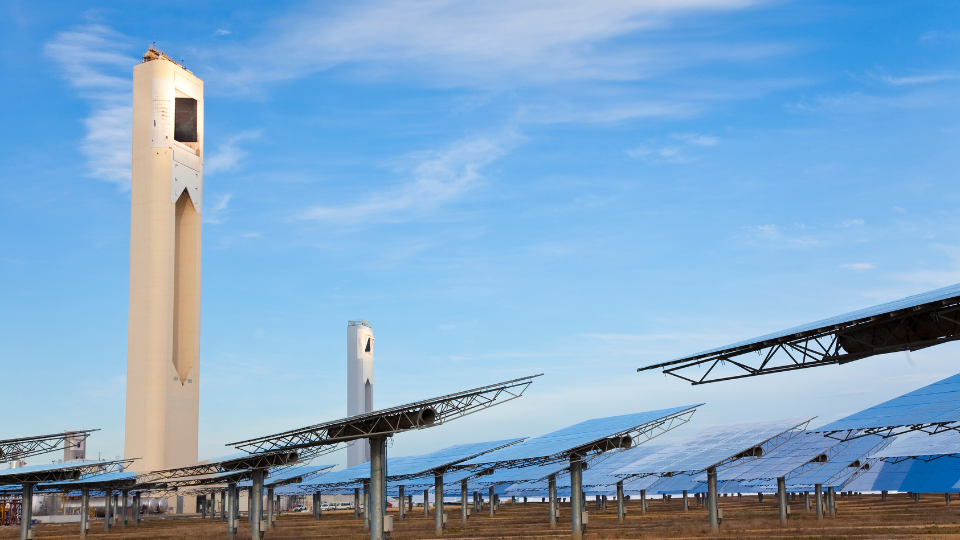
Halbleiterlithographie: EUV-Licht im Ultrahochvakuum lenken
Ein weiterer Anwendungsbereich für Spiegelablenksysteme ist die Halbleiterlithographie zur Fertigung von Computerchips. Aufgrund der Miniaturisierung von Computerchips bei immer höherer Leistungsfähigkeit müssen extrem winzige Strukturen auf den Silizium-Wafer aufgebracht werden. Dies geschieht inzwischen mit sehr kurzwelligem UV-Licht – EUV, also extrem ultraviolettem Licht –, das nur über besonders glatte Spezialspiegel abgelenkt werden kann. Übliche Linsen könnten das UV-Licht nicht mehr richtig fokussieren. Die Ausrichtung der Spiegel muss dabei hochgenau im Nanometerbereich funktionieren und stellt entsprechend hohe Anforderungen an die Präzision der Positionssensoren. In der Regel kommen hier kapazitive Sensoren zum Einsatz, die in einem sehr kleinen Messbereich hochgenaue Ergebnisse erzielen und die sich nicht von teilweise in der Lithographie genutzten starken Magnetfeldern beeinflussen lassen – induktive Sensoren können in diesen Fällen nicht eingesetzt werden.
Auch in diesem Beispiel stellen die Umgebungsbedingungen besondere Herausforderungen. Die Wafer-Produktion erfolgt im Ultrahochvakuum, was Elektroniken und Schaltungen hinsichtlich des geringen Drucks aushalten müssen. Diese dürfen nicht ausgasen und so schädliche Stoffe in das System einbringen. Die verwendeten Materialien müssen also entsprechend den Vakuumanforderungen ausgewählt werden. Kritisch ist beispielsweise, wenn elementarer Wasserstoff entsteht. Dieser kann die Komponenten selbst zersetzen und die Maschine schädigen, da er chemisch sehr aggressiv ist.
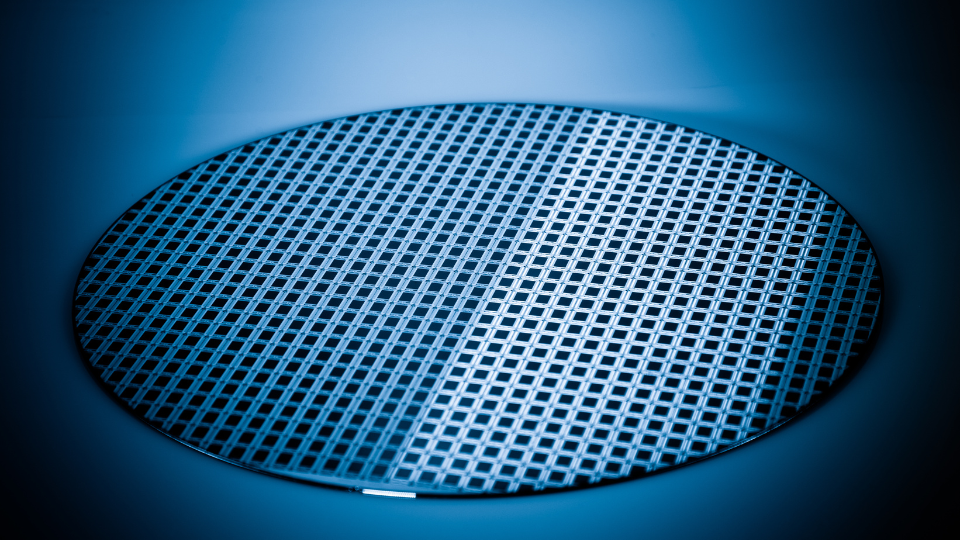
Hochgenaue Sensoren für besondere Anforderungen
Wenn es um hochgenaue Abstandsmessungen geht, die in Spiegellenksystemen zur präzisen Ausrichtung der Spiegelflächen dienen, sind das induktive und das kapazitive Messsystem die Messprinzipien der Wahl. Induktive Sensoren sind schmutzunempfindlich; Staub und Feuchte haben keinen Einfluss auf das Messergebnis. Erzeugt wird ein elektromagnetisches Feld, in das ein metallisches Gegenstück eingebracht wird, durch das das Feld abgeschwächt wird. Die Abschwächung des Feldes lässt sich messen und korreliert mit der Objektgröße, dem Objektmaterial und auch mit dem Abstand. Wenn Material und Größe weitgehend konstant gehalten werden, aber der Abstand geändert wird, lässt sich der induktive Sensor als Abstandssensor nutzen.
Beim kapazitiven Messsystem ist nicht zwingend ein metallisches Gegenstück notwendig; auch nicht-metallische Werkstoffe lassen sich mit kapazitiven Sensoren messen – und das in kleinsten Toleranzen im Nanometerbereich. Der Aufbau besteht aus einer Fläche, auf die Ladung gebracht wird, und einer Gegenfläche, die die Platten eines elektrischen Kondensators bilden. Die Kapazität dieses Aufbaus wird gemessen. Auch dies ist abstandsabhängig; wenn sich der Abstand verringert, ändert sich auch die Kapazität. Dieses Messsignal lässt sich als Abstand interpretieren. Winzige Veränderungen können so detektiert werden und für den speziellen Anwendungsfall der Spiegelausrichtung genutzt werden.
Entscheidend für die Funktionalität der Sensoren sind dabei präzise Elektroniken, die temperaturstabil und robust genug sind, um den harschen Umgebungsbedingungen in Wüste, Weltraum und Vakuum standzuhalten.
Für diese anspruchsvollen Anwendungen bietet die LTCC Mehrlagen-Keramiktechnologie von Micro-Hybrid einzigartige Lösungen.
Wir beraten Sie gern zu Ihrem Entwicklungsprojekt und den optimalen Substrat- und Packagingtechnologien.